Aluminium Heat Seat
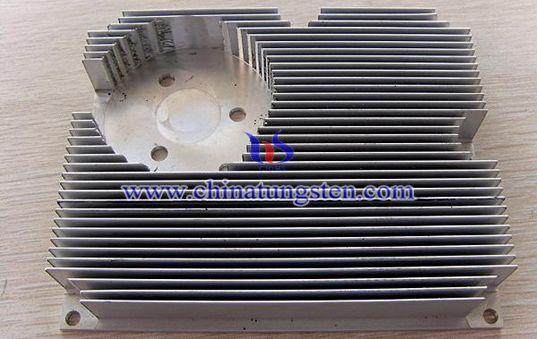
Sheets smaller and higher efficiency than the traditional heat seat
Al Heat Sink
Material : Al 99.5% or copper
200% efficiency, save 50% space
Much smaller and higher radiating efficiency than the traditional heat seat
Radiating efficiency
Much smaller size than traditional heat seat
Sheet thickness: 0.15mm-0.2mm
Each sheets gap in length and width: 0.3mm
The most common heat seat material is aluminium. Chemically pure aluminium is not used in the manufacture of heat seat, but rather aluminium alloys. Al alloy has one of the higher thermal conductivity values at 229 W/m•K. However, it is not recommended for machining, since it is a relatively soft material. Al alloys 6061 and 6063 are the more commonly used aluminium alloys, with thermal conductivity values of 166 and 201 W/m•K, respectively. The aforementioned values are dependent on the temper of the alloy.
Copper is also used since it has around twice the conductivity of aluminium, but is three times as heavy as aluminium copper is also around four to six times more expensive than aluminium, but this is market dependent. Copper and aluminium prices can be compared on Internet websites, such as the London Metal Exchange. Aluminium has the added advantage that it is able to be extruded, while copper can not. Copper heat sinks are machined and skived. Another method of manufacture is to solder the fins into the heat seat base.
Another heat seat material that can be used is diamond. With a value of 2000 W/mk it exceeds that of copper by a factor of five. In contrast to metals, where heat is conducted by delocalized electrons, lattice vibrations are responsible for diamond's very high thermal conductivity. For thermal management applications, the outstanding thermal conductivity and diffusivity of diamond is an essential. Nowadays CVD diamond is used as submounts for high-power integrated circuits and laser diodes.